Rebuilding

CNC MACHINE REBUILDING SERVICES
At MTB we look at rebuilding a machine like doing a frame off restoration of your classic car, but with a new high performance engine and chassis nestled underneath the body. Nothing is left untouched, every active component is upgraded, every mechanical piece meticulously inspected then repaired or replaced.
Like your classic, even the paint is given special treatment by painting before assembly to insure complete coverage and adhesion. Instead of new brake lines, we are installing new custom made hydraulic lines, for the electrical systems we install all new wiring throughout the machine, drive trains are shortened for efficiency and accuracy, and finally a new high output engine (The CNC) is installed and tuned to give peak performance to your new machine.

Featured Rebuilds
Pfauter P400H Bucyrus International
This machine was a complete rebuild of a Pfauter P400H with a 4 meter long bed. This machine was originally a fully mechanical machine with index and differential change gears. We converted the machine to a full 5 axis CNC machine with one spindle, X (radial), B (cutter rotation), C (table rotation), Y (Tangential), Z (Axial), A (hob head swivel) and the programmable spindle speed. The controls were GE Fanuc 18i-MB with Alpha Hvi digital servos and spindle.
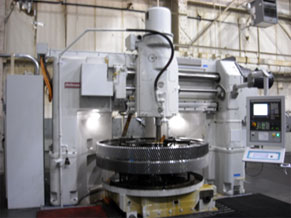
Fellows 60-15 Horsburgh and Scott
This machine was a complete rebuild of a Fellows 60-15. We converted the mechanical machine into a 5 axis fully CNC controlled machine, X (infeed), B (cutter rotation), C (table rotation), Z (elevation and stroke), X2 (Backoff Cam). We removed the entire mechanical drive train for the stroking motion and installed a 2000Nm Siemens torque motor on the rocker shaft to directly control the up/down stroke motion. This allowed us to implement independent feed rates for the down stroke and up stroke. It was a huge cycle time savings for the customer by allowing a full speed upstroke and slow cutting down stroke. Also the torque motor concept allowed us to have a programmable elevation, which saved time in doing internal gears. The controls we installed were Siemens 840D with PCU 50 front end and our custom conversational gear shaping program.
Fellows FS400 – 125 Caterpillar
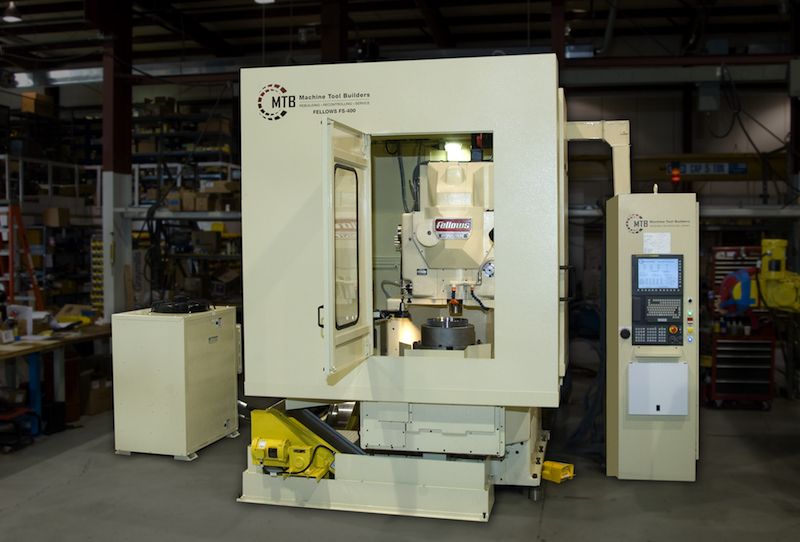
This machine was a complete rebuild of a Fellows FS400-125. This machine was a 6 axis and one spindle machine, X (infeed), B (cutter rotation), C (table rotation), Z (elevation), W (Stroke length), T (Tool magazine) and the programmable spindle speed. The machine had an 8 position tool turret and was designed to shape four consecutive surfaces by changing up to four tools in succession. The controls were Siemens 840D with PC front end.